Inside the exclusive Bugatti Atelier: how the world’s most luxurious supercars are made
- Bugatti Atelier is the ultimate supercar HQ, located in France
- Molshiem has played host to Bugatti for over a century
- But the new HQ is a masterclass in efficiency
Published by Jack Marsh
Edited by Tom Wood
Bugatti Atelier is the foundation on which the pinnacle of supercar manufacturing was created.
But the French factory has many secrets behind its doors.
With world-renowned supercars like the timeless Veyron and record-holding Chiron coming from within, Bugatti’s special HQ is truly one of a kind.
So what lies behind the doors of the esteemed Bugatti Atelier? Well, for starters, the next wave of bespoke supercars hand-crafted by a tiny range of geniuses.
VISIT SBX CARS – View live supercar auctions powered by Supercar Blondie
Where are supercars from Bugatti made?
As a leading supercar designer from Europe, Bugatti hails from Molsheim, France.
Since Ettore Bugatti started creating the Type 10 back in 1909, almost every stitch of interior leather and exterior carbon fiber has been sewn in the town in eastern France.
Only a brief 11-year stint between 1987-98 saw production shift to Italy under the Volkswagen parent banner, which saw the development of the EB 110 model and its spin-off 112 concept.
For the most part, though, Molsheim has played host to Bugatti, where the Atelier factory was built in the early 2000s on the same grounds as the family mansion.
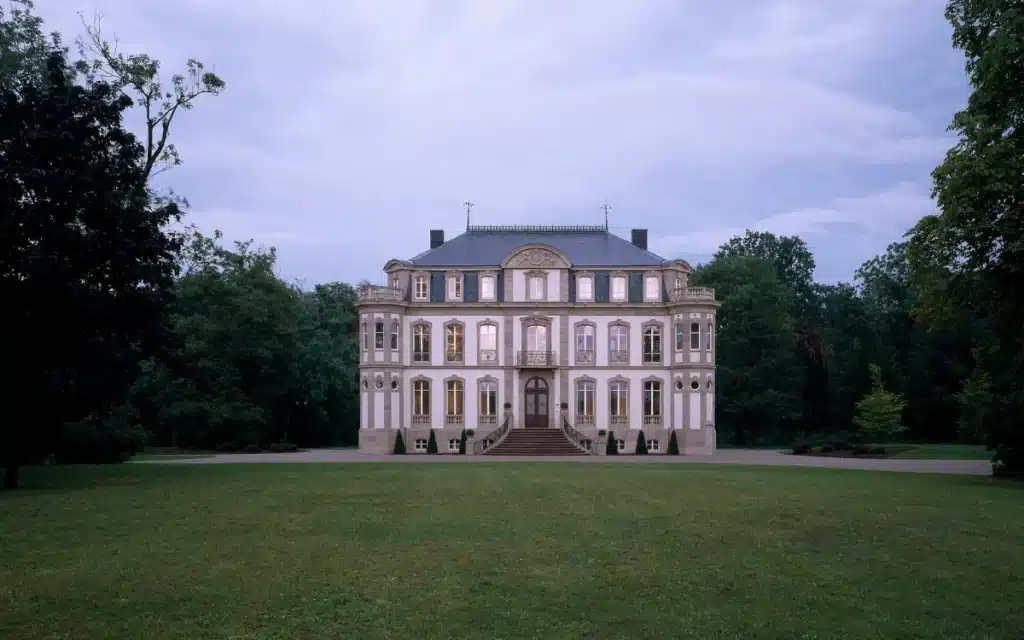
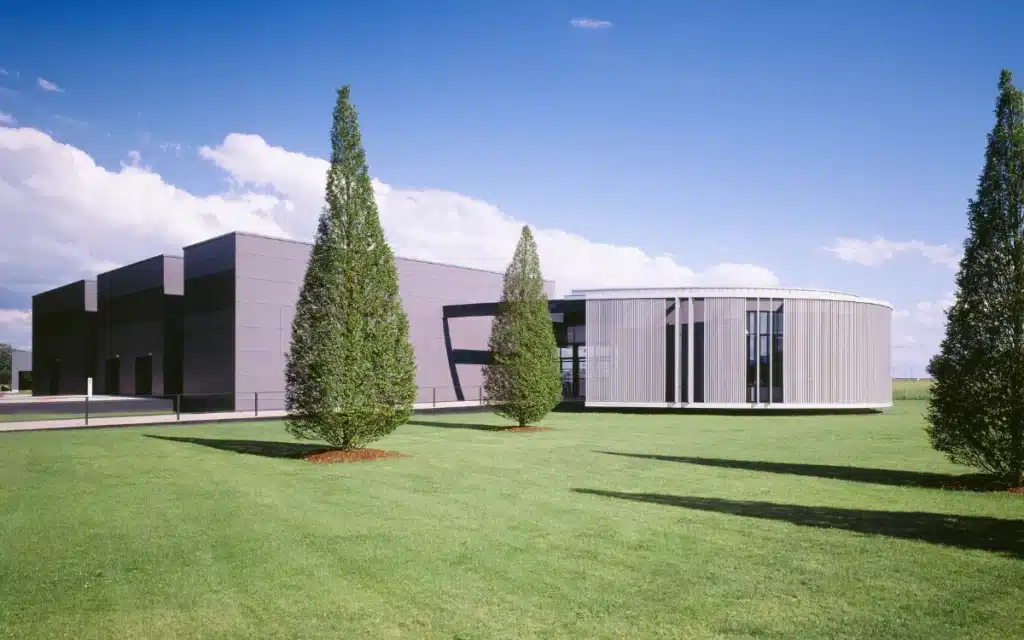
Looking more like a blend between a Victorian farmyard and a sci-fi doomsday den rather than a typical garage, the Atelier is very much reciprocating the class, precision, and character that goes into each Bugatti supercar that is produced within it.
To this day, Bugatti is currently adding the finishing touches to multiple of the first Tourbillon orders while running the magnificent and meticulous tests for the track-ready Bolide.
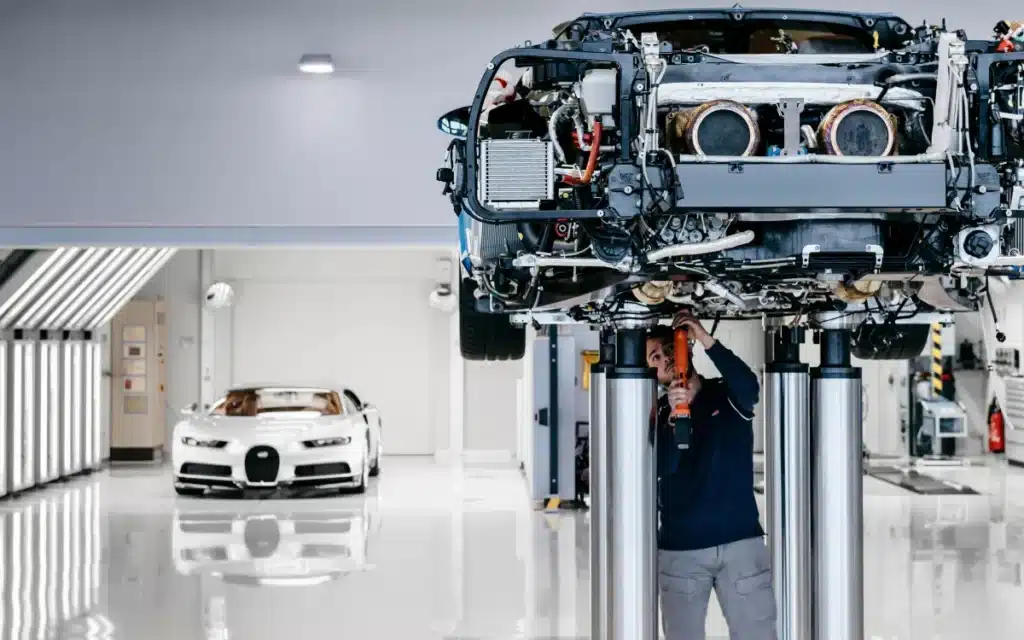
Inside the Bugatti Atelier
Unlike other supercar HQs, such as the McLaren self-shrine in Woking, UK, the Bugatti Atelier isn’t much of a museum piece and is rather just an efficient dome of manufacturing brilliance.
Instead, a small team works within the factory.
It’s just 1,000 square meters (the rough size of four houses in a square), and there are no robots—everything is made by hand, showcasing a new range of efficiency.
Only 20 people were involved in the development of the Chiron, as a select few mechanics and engineers assembled the 1,800 pieces of metal to create the fastest car the world has ever seen.
They work at 12 stations, ranging from engine creation to testing to interior design, with each member of the team knowing exactly what is underneath the hood.
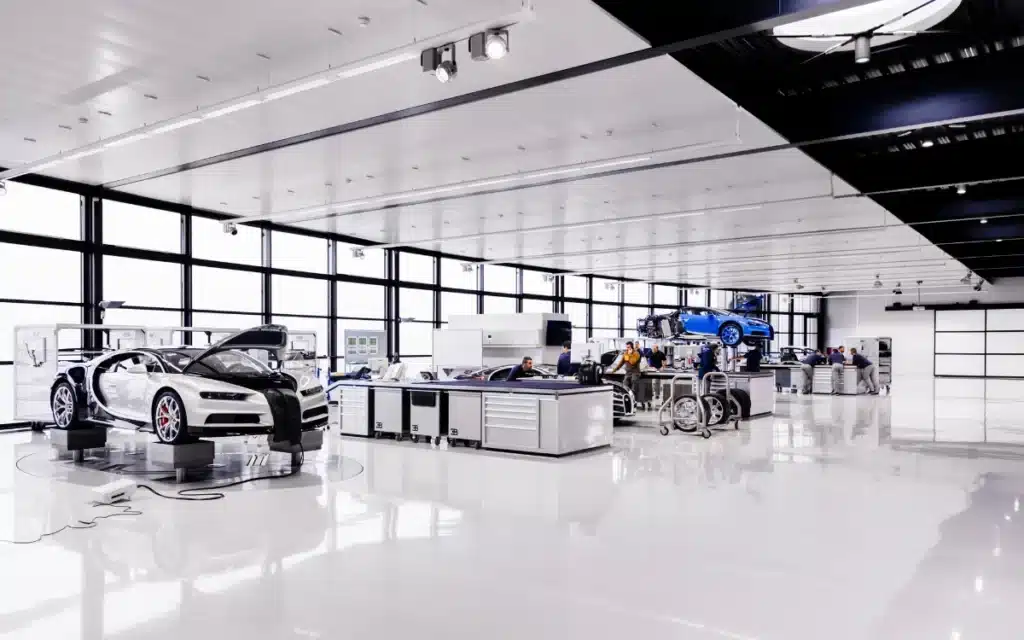
This process was documented for the Chiron creation, but similar processes have been used for the new Mistral, Tourbillon, and Bolide.
“Here in Molsheim, we have a small factory with a small warehouse. Neither our equipment nor our procedures can be compared with those of other car plants,” said Christophe Piochon, Head of Production and Logistics.
With the new supercar ranges gearing up to roll out of the factory this year, the small team is in for a serious graft.
But at least they can work in style at this stunning HQ.
DISCOVER SBX CARS: The global premium car auction platform powered by Supercar Blondie